The Duty of Metal Stamping in Modern Production and Product Advancement
The Duty of Metal Stamping in Modern Production and Product Advancement
Blog Article
Advanced Techniques in Metal Stamping for Precision Manufacturing
In the realm of precision production, the development of steel marking techniques has been a crucial force in achieving unrivaled degrees of accuracy and performance. As markets constantly require finer resistances and elaborate layouts in their metal components, the mission for advanced methods in metal stamping has heightened. From the utilization of advanced multi-stage marking processes to the assimilation of advanced automation technologies, the landscape of steel marking is going through an extensive transformation. In this vibrant sector, the convergence of technology and accuracy is improving the possibilities of what can be accomplished in metal construction.
Advanced Multi-Stage Stamping Processes
Going over the details of advanced multi-stage stamping processes reveals the advanced strategies used in modern-day production techniques. Metal Stamping. Multi-stage stamping is an intricate process that includes several steps to transform a flat sheet of steel right into a last stamped item. The usage of dynamic passes away, where various procedures are done at each stage of the stamping process, allows for high accuracy and performance in the manufacturing of intricate steel components
Throughout the preliminary phases of multi-stage marking, the level metal sheet is fed into the stamping press, where a series of passes away are made use of to reduce and shape the material. Subsequent stages entail added developing, flexing, and punching procedures to additional refine the part. Each phase is meticulously created to build upon the previous one, leading to the creation of complex geometries with limited resistances.
Advanced multi-stage stamping processes call for a high degree of expertise and accuracy to make sure the high quality and consistency of the stamped components. By making use of advanced machinery and tooling, suppliers can create a broad range of steel elements with efficiency and accuracy.
Precision Tooling Innovations
Precision tooling technologies have revolutionized the metal marking sector, boosting effectiveness and quality in producing processes. These innovations have dramatically impacted the way steel components are generated, resulting in higher accuracy and consistency in the last products. One vital development is the growth of computer mathematical control (CNC) technology in tooling layout and fabrication. CNC systems enable intricate styles to be equated directly right into tooling, ensuring accuracy and repeatability in the marking process.
Additionally, the combination of sensors and real-time monitoring capabilities in precision tooling has allowed makers to spot and deal with problems quickly, lessening downtime and minimizing scrap prices. By integrating wise innovation into tooling, operators can optimize parameters such as pressure, rate, and positioning during the marking procedure, leading to enhanced product high quality and boosted productivity.
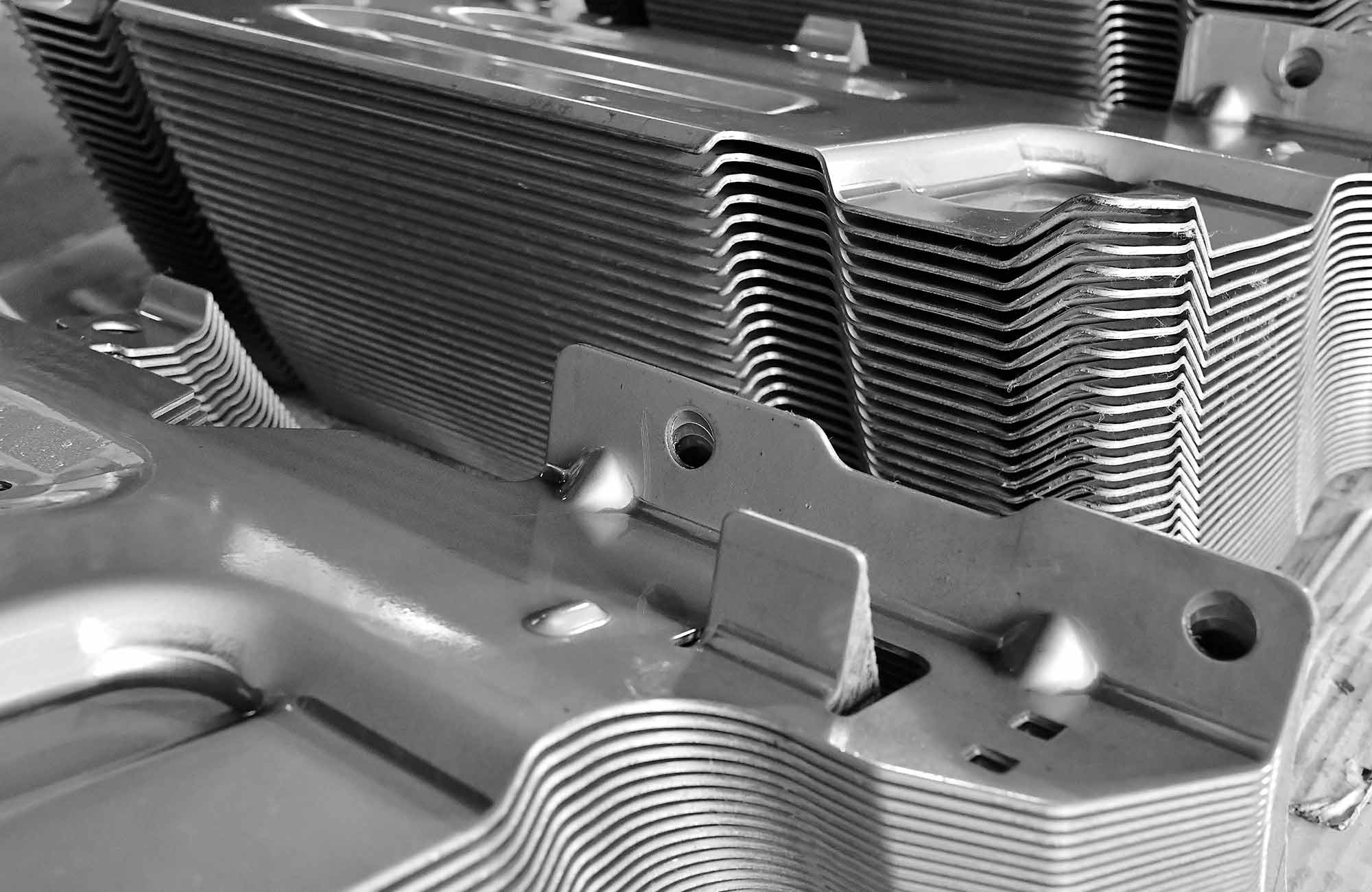
Automation in Metal Stamping
The development of accuracy tooling innovations in the steel marking sector has actually led the way for significant advancements in automation, transforming the production landscape in the direction of boosted effectiveness and productivity. Metal Stamping. Automation in metal marking great post to read includes using innovative machinery and robotics to perform numerous jobs typically accomplished by human drivers. This change towards automation offers countless advantages, including boosted precision, faster manufacturing cycles, and minimized labor costs
One trick element of automation in metal marking is the application of computer mathematical control (CNC) systems, which allow precise control over the marking process. CNC modern technology enables the creation of facility and elaborate steel get rid of regular high quality. Additionally, automated systems can be programmed to run continuously, causing higher outcome prices and shorter preparations.
Furthermore, automation boosts workplace security by reducing manual handling of hefty products and reducing the threat of accidents (Metal Stamping). As producing sectors remain to welcome automation, the future of steel stamping holds excellent promise for also better efficiency and advancement
High-Speed Stamping Techniques
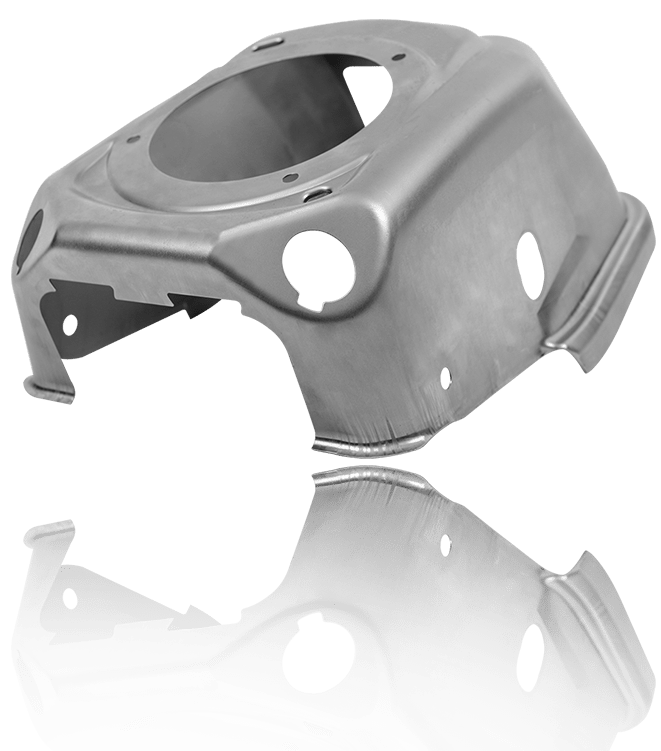
Among the main advantages of high-speed marking techniques is the capability to create a huge quantity of components in a much shorter quantity of time contrasted to standard marking approaches. This raised performance not just permits suppliers to fulfill limited production due dates yet additionally allows expense savings with economies of scale. Additionally, high-speed stamping can help in reducing product waste by enhancing the material usage during the stamping procedure.
In addition, high-speed marking methods typically integrate ingenious features such as quick die adjustment systems and real-time tracking capabilities, further boosting the total efficiency and adaptability of the steel stamping procedure. As modern technology continues to advancement, high-speed stamping is expected to play an important role in driving the future of accuracy manufacturing.
Quality Control in Stamping Procedures
Reliable quality assurance steps are important for ensuring the dependability and consistency of steel stamping procedures. Quality control in marking procedures involves a collection of systematic procedures targeted at identifying and protecting against problems in the made elements. One crucial element of quality control in steel stamping is making use of innovative assessment methods such as optical assessment systems and coordinate determining devices (CMMs) to validate the dimensions and resistances of stamped components.
Additionally, quality assurance steps in marking operations usually include the application of analytical procedure control (copyright) methods to keep track of the manufacturing process in real-time and guarantee that it continues to be within acceptable limits. By examining information and recognizing fads, makers can proactively resolve any discrepancies from the wanted top quality requirements.
In addition, quality control in metal stamping procedures additionally entails comprehensive product testing to guarantee that the raw materials utilized satisfy the called for requirements for the marking procedure. Your Domain Name This may include conducting material hardness tests, tensile stamina tests, and dimensional evaluations to guarantee the high quality and stability of the stamped elements. Generally, applying durable quality assurance actions is crucial for achieving top quality stamped parts consistently.
Conclusion
To conclude, advanced techniques in steel marking play a critical role in accuracy manufacturing processes. With multi-stage stamping processes, innovative tooling remedies, automation, high-speed strategies, and extensive quality assurance steps, producers can attain greater levels of accuracy and performance in their procedures. These developments in steel stamping innovation have made it possible for firms to create complicated parts with tight resistances, eventually leading to boosted item quality and consumer contentment in the production industry.
Report this page